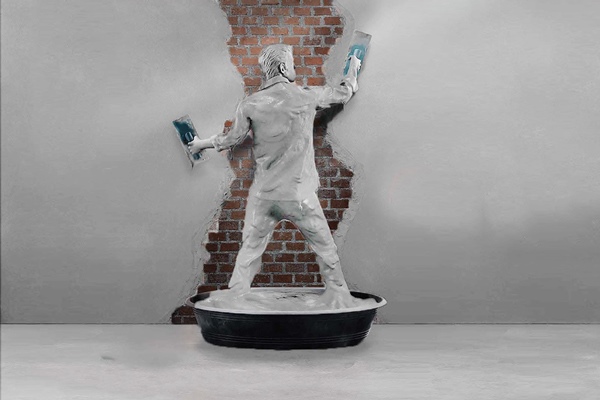
Coats properties in plastering
Thickness and numbers of coats in plastering
Plastering, a critical aspect of finishing work, relies on multiple coats and precise layer thicknesses to ensure a smooth, durable surface. Proper application involves understanding both coat composition and setting times to avoid common issues like cracking, detachment, or uneven surfaces.
1. Thickness and Number of Coats in Plastering
- Base Coats: For effective plastering, a minimum of three coats should be applied. The standard thickness is typically 2.5 cm or greater, with each layer adding stability and strength.
- Layer Composition: The first coat often uses a gypsum-soil mixture with a thickness of about 1.5 cm, providing a robust foundation. The following coat—usually stucco—adds an additional 1 cm, while a final polish coat, or “killed plaster,” requires only 2 mm for a smooth, refined finish.
2. Setting Times and Coat Properties
- Quick-Setting Plaster: Also known as adamant plaster, this type begins setting within 2 minutes and fully sets in about 15 minutes. Ideal for projects needing quick turnaround, this type ensures a firm base quickly but requires careful timing.
- Normal-Setting Plaster: With a setting time of about 6 hours, this is suited for standard applications where gradual drying reduces the risk of surface cracks.
- Retarded or Slow-Setting Plaster: Slowed by additives like hydrated lime (usually 10% of the plaster’s weight), this type takes up to 20 minutes to start setting, allowing for adjustments during application.
3. Using Lime to Adjust Setting Times
Adding lime can extend the setting time up to 12 minutes, creating a slower drying process ideal for large or complex surfaces. To ensure smooth consistency, lime slurry should pass through a fine sieve (mesh less than 1 mm) to prevent clumps that may affect coat integrity.
4. Coat Materials and Surface Preparation
Adequate gypsum mortar includes combinations like thatch mortar, gypsum-soil mixes, or grit-enhanced mortars for different levels of adhesion and durability. Key surface conditions—absence of ripples, cracks, and roughness—are essential for achieving an even, flawless finish.
5. Preventing Cracks and Surface Defects
- Layer Firmness: Ensure each coat dries completely before applying the next. Applying plaster to a wet or partially set layer increases the risk of cracking, detachment, or rippling.
- Gradual Application: Thick layers should not be applied all at once; instead, build them up gradually to prevent stress within the material that can lead to surface cracks.
6. Finishing Touches for Polished Surfaces
For smooth and light-reflective coats, extra care should be taken with precision and timing. Polished coats intensify light and highlight imperfections, so surface preparation and even, careful application are essential for a high-quality finish.
By following these guidelines, you can achieve a reliable, aesthetically pleasing plastered surface that is resilient against environmental stress and time